Hidden costs associated with downtime: why sausage clips reliability will be crucial in 2025
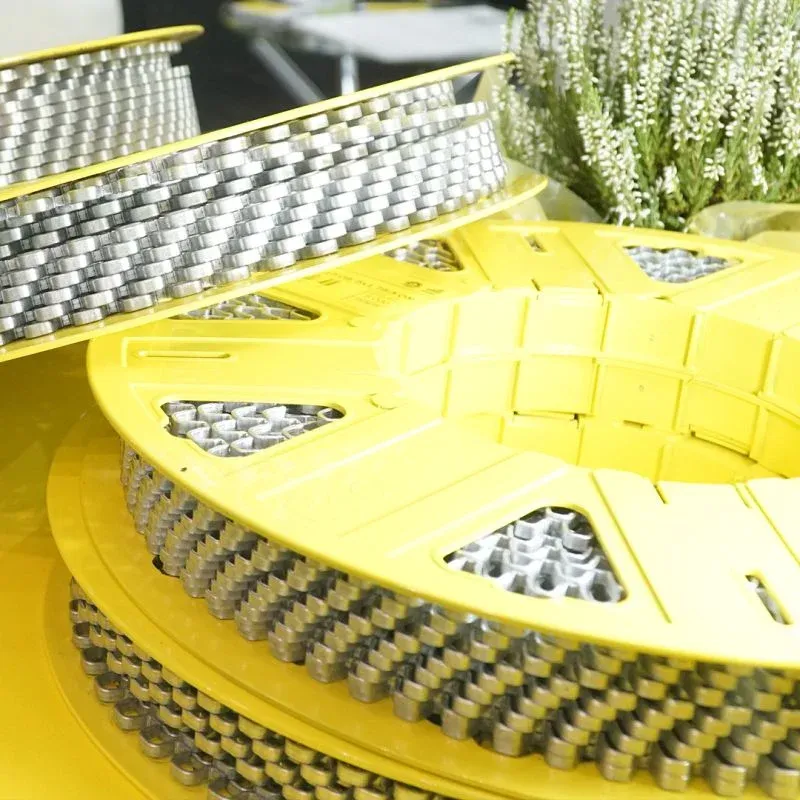
Hidden costs associated with downtime: why sausage clips reliability will be crucial in 2025
When assessing risks at any business, we all try to cover as much ground as possible to identify all potential problems. For example, when you think about what could stop a sausage production line, the first things that come to mind are:
- equipment failure
- lack of casings
- Staffing issues
But if you look closer, you can see that the lack of high-quality small metal clips can cause a big problem. And this is not a hidden threat, it is a real problem that will cost North American meat producers thousands of dollars every week.
Unreliable sausage clips.
They may seem like a small thing, but clips are a critical consumable, and their quality (or lack thereof) directly affects uptime, product quality, and safety.
A $0.03 Part That Can Create a $3,000 Problem
Let’s break it down:
- Your line runs at 200 sausages/min
- One bad clip jams the machine
- Your line stops for 45 minutes
- You lose a full pallet of product due to rework or rejection
- Tech team gets pulled off another task
- QA flags a casing tear or loose seal
Total cost? Easily $2,000–$5,000 in lost value, depending on the product and timing.
All because a single clip broke, jammed, or failed to close.
What does “unreliable” really mean?
We think that a reliable supplier will always have reliable clips, but let's think about what buying low-quality or non-standard clips can lead to. Here are a few things that can happen:
- Incorrect feeding into the clipper rail
- Incomplete or cracked closure
- Product contamination from excess dust from the clips
- Sharp edges that damage natural or collagen casings
- Uneven seal strength during vacuum packaging
This is just a small list of what can happen, and I can tell you that these are not minor problems — they are huge production risks.
Why does this happen — and how can it be avoided?
- In fact, there are many problems that can cause downtime, for example:
- Incompatibility of aluminum alloy or mold
- Poor condition of tools or coating
- Low casting accuracy
- Incorrect size/code of the clamp for your equipment
Logical question then follows: how can this be fixed or prevented?
Answer is simple: only work with proven clip suppliers or those who have references from other manufacturers. This selection method will help you avoid unpleasant consequences in the future.
I would like to speak on behalf of KOMPO North America Inc. We have been in the market for 13 years with our own production of clips that fit any clip applicator on the Canadian and US markets. We have almost everything, no matter what brand of clipper you use in your work. Companies such as KOMPO North America Inc. offer:
Clip codes suitable for machines of any brand - our clips will fit any clipper, and the price will be 30-40 percent lower.
Food-grade aluminum - high-quality aluminum, specially formulated for us and with unique properties.
Free samples so you can evaluate performance before switching to a new product.
Hidden return on investment in high-quality clips
Do you think that changing clips only has obvious advantages?
Have you considered what you get with new clips?
- Fewer jams
- Less downtime
- Better sealing
- Lower maintenance costs
- A happier quality control team
- More consistent batch output
And don't forget one more thing: if you are being audited (BRC, SQF, or private label), poor clip performance = red flags in your documentation.
Last Thought
In 2025, meat processors know:
“You don’t buy clips. You buy peace of mind.”
So next time you’re sourcing consumables, don’t just ask:
“How much per box?”
Ask:
“How much will this clip cost me if it fails?”